Materials Tech Pulse
SEPS vs SEBS | Compare Thermoplastic Elastomers for Product Development
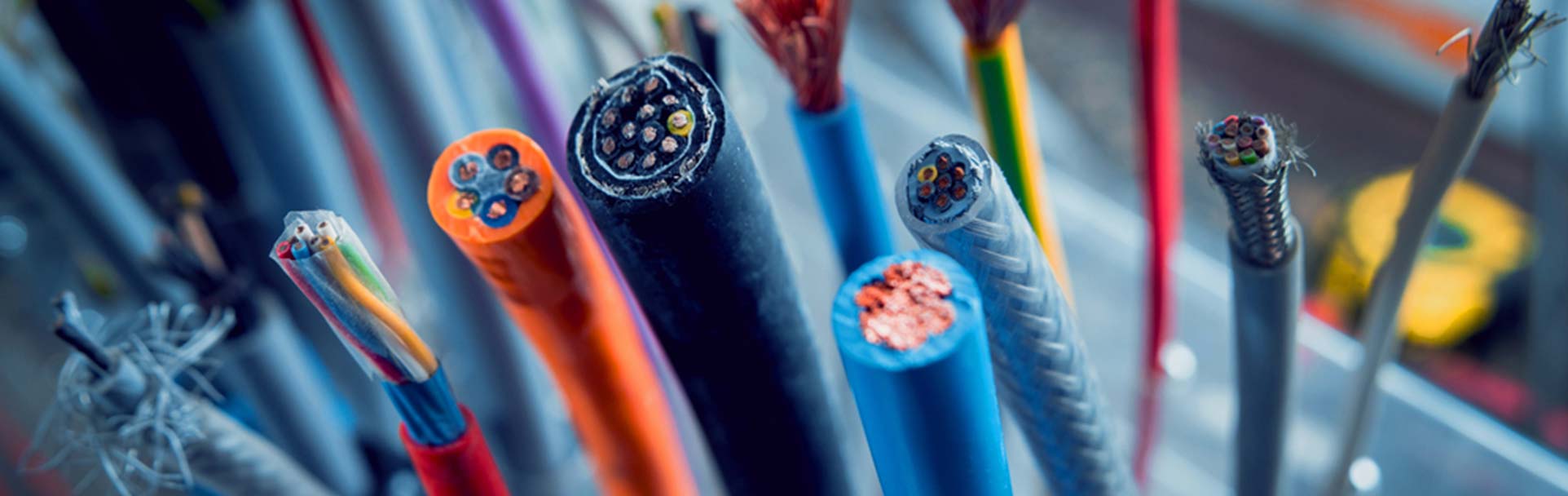
The convenience offered by petrochemical products has made them an indispensable part of our lives. Plastic materials such as PP, PE, nylon, and ABS are found in our everyday products.
To achieve a more effective use of our natural resources, the industry continues to refine the technology and efficiency of the recycling process and has expanded the development of reclaimed products in recent years. The goal is to save resources and reduce the impact on the environment.
Crushed PP and PE plastics are melted after recycling; SEBS and SEPS are added during the compounding process to effectively increase the impact resistance of the end plastic products.
The physical properties differences between SEPS and SEBS Polymer (Using Grade 8501U as an Example of SEPS)
Based on the information provided in the table above, SEBS grade 9901 demonstrates excellent performance across properties, making it the top choice for material modification. It can also be used in automotive and PA modification and ABS over-molding applications.
On the other hand, SEBS grade 9552/U provides balanced mechanical properties and is highly compatible with PO, PP, and PE materials. Its excellent strength makes it a suitable candidate for plastic modification, coating and adhesive application.
SEBS grade 9557D has a higher percentage of double block copolymers, which leads to higher performance in terms of softness and flexibility. This property makes 9557D suitable for adhesives, co-extrusion film, coatings and plastic modification applications.
What is SEPS polymer and SEBS used for?
In short, SEPS is the top choice for transparency, while SEBS is your pick for outdoor products
SEBS and SEPS are hydrogenated styrene block copolymers (HSBC) within the TPE class. HSBCs consist of styrene-based hard blocks and a hydrogenated diene soft block. HSBCs exhibit rubber-like elasticity, excellent heat and weather resistance, and are highly compatible with PP and PE plastics.
- SEPS (styrene ethylene propylene styrene):known for its transparency and is applied in a wide range of transparent products, but is not ideal for printing. SEPS has a high oil absorption ratio and can maintain dry, comfortable and non-sticky surface even after being filled with large quantities of rubber oil. Certain grades demonstrate better superior transparent, softness and toughness after oil extension, giving them an even wider range of applications.
- SEBS (Styrene-ethylene-butylene-styrene):contains some hydrogenated butadiene in its structure. More hydrogenated butadiene increases material strength, enhances the sturdiness of the finished products, and is less prone to the effects of UV rays and oxidation. SEBS is more commonly applied in outdoor products. It has excellent aging resistance, oil extension and temperature resistance. However, it has balanced physical performances.
The difference between the application of SEPS and SEBS
Note: “◎” suitable for applications that require transparency
SEBS is commonly applied in handles, wire and cable cladding and the automotive industry. Different SEBS grades have varied ranges of applications depending on their physical properties.
SEPS is applied in oil modification, candle gel , and superior transparent application, etc. due to its high physical performance. It can also be used in transparent gel candles and transparent plastic modification given its transparent appearance; SEPS is used as a modifier for PP plastic modifier.
As the frontrunner in sustainable rubber solutions, LCY offers the best SEBS and SEPS materials
SEBS and SEPS boast a wide range of applications with versatile physical properties that meet the demand of an array of industries. LCY understands that industries have specific requirements for material quality and safety. We offer informational data and safety specifications for all of our products.
View the physical properties and safety specifications for SEBS and SEPS before selecting the material that is right for you. Or contact us to share your expectations on product structure and mechanical property and our team will guide you through the selection process.